Products
Assembly jig
AUTOMOTIVE WELDING JIG MACHINERY
This device regulates the positioning of parts to enable precision welding of sheet metal components for vehicle bodies.
The welding jig ensures high quality by maximizing the use of 3D CAD, offline teaching.
※Click on the image to enlarge.
Hemming apparatus
HEMMING MACHINERY
This apparatus is ideal for small production volumes, utilizing a robot roller system.
It offers flexibility, accommodating low capital investment and model changes.
The equipment cost is reduced to approximately 1/50 compared to a conventional large press machine for hemming.
The robot is equipped with a lower die for hemming, jigs to secure the outer and inner panels, and hemming rollers.
Two robots can operate simultaneously for increased output.
Due to its flexibility, the robot can hem hoods, left/right front/rear doors, and back doors simply by replacing the dies and jigs.
This robot is optimal for small-lot production and can easily adapt to remodeling needs.
※Click on the image to enlarge.
T/T (table top) Hemming
HEMMING MACHINERY
The T/T Hemming machinery operates a C-shaped frame with a blade using hydraulic force, making it ideal for medium production volumes.
Our T/T Hemming machine is designed for forming automobile cover parts in medium lots.
This machine allows hemming in a significantly smaller space compared to conventional machines.
While a large press machine is typically used for hemming, press hemming has disadvantages such as high equipment investment costs for the press machine and dies.
Additionally, die replacement in lot production is time-consuming.
It is also necessary to supply cover parts for up to 10 years after production ceases, which requires sufficient storage space for the dies.
In T/T Hemming, the outer and inner panels are placed on the lower die and lifted hydraulically against a C-shaped frame, which features pre-bending and full bending blades for caulking.
The equipment investment for tabletop hemming is approximately half that of press hemming, and the equipment area required is much smaller.
※Click on the image to enlarge.
Press Hemming
HEMMING MACHINERY
The press hemming system utilizes a pressing machine and is ideal for mass production.
We propose a press hemming method that is optimized for mass production, offering excellent cost-effectiveness.
A cam mechanism is fully employed to complete both pre-hemming and full hemming with a single stroke, reducing the overall pressing process.
This approach not only reduces the initial investment in dies but also lowers the product cost by streamlining the pressing process.
※Click on the image to enlarge.
Circular cutter
GENERAL INDUSTRIAL MACHINERY
In the process of film manufacturing, film end materials that are not suitable for use as products are generated.
This machine cuts these film end materials into chips for recycling.
The film manufacturing process involves gradually winding a soft resin sheet while pulling it sideways to achieve a thickness of approximately 0.0001 mm.
The areas where the film is clamped for sideways pulling, as well as the non-standard parts at the beginning of the winding, become waste.
This circular cutter efficiently cuts these non-standard film parts into chips for recycling.
Our company possesses extensive know-how regarding the shape of the film cutting blade and how to secure the blade clearance.
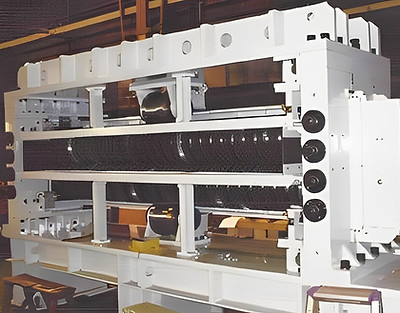
High speed seater
GENERAL INDUSTRIAL MACHINERY
This high-speed seating device for automotive applications is based on our extensive experience and expertise.
The system is adaptable to various materials and operates efficiently at high speeds.
The automatic adjustment mechanism reduces maintenance needs and improves operational efficiency.
The seating capacity and handling capabilities enhance overall productivity.
We can accommodate various design and layout requirements to meet your specific needs.

FLOOR MAIN Welding Line
GENERAL INDUSTRIAL MACHINERY